Choose the PPE gloves standard
EN 388:Protective gloves against mechanical risks
To help users and safety managers determine the level of protection for a pair of gloves, EN 388:2016 uses index values to evaluate how well a glove performs against various mechanical hazards. These include abrasion, blade cuts, tears, punctures and impacts. The 2016 edition of the standard enables you to better match the protection you need against the hazards present in your work environment.
About EN 388 Mark:Gloves with a EN 388 rating are third party tested, and rated for abrasion, cut, tear, and puncture resistance. All tests must be performed on the material in the palm area of the glove and the combination of materials used in glove construction.
Protection against mechanical hazards is indicated by a pictogram followed by four numbers (i.e. performance class), each number representing the test performance against a specific hazard:
A - Abrasion resistance
Based on the number of cycles required to abrade the sample glove (e.g., abrade with sandpaper at a specified pressure). The protection factor is then expressed on a scale of 1 to 4 based on the number of revolutions required to make a hole in the material. The higher the number, the better the protection (see table below.)
B - Blade Cutting Resistance
Based on the number of cycles required to cut a sample glove at a constant speed. The protection factor is then expressed on a scale of 1 to 5.
C - Tear Resistance
Based on the amount of force required to tear the sample. The protection factor is then expressed on a scale of 1 to 4.
D - Puncture Resistance
Based on the amount of force required to pierce a sample with a standard sized tip. The protection factor is then expressed on a scale of 1 to 4.
NOTE: A result marked with an X indicates that the glove was not tested for the hazard; it was not tested; a result marked with an O indicates that the glove failed the test.
About EN 388 Mark:Gloves with a EN 388 rating are third party tested, and rated for abrasion, cut, tear, and puncture resistance. All tests must be performed on the material in the palm area of the glove and the combination of materials used in glove construction.
Protection against mechanical hazards is indicated by a pictogram followed by four numbers (i.e. performance class), each number representing the test performance against a specific hazard:
A - Abrasion resistance
Based on the number of cycles required to abrade the sample glove (e.g., abrade with sandpaper at a specified pressure). The protection factor is then expressed on a scale of 1 to 4 based on the number of revolutions required to make a hole in the material. The higher the number, the better the protection (see table below.)
B - Blade Cutting Resistance
Based on the number of cycles required to cut a sample glove at a constant speed. The protection factor is then expressed on a scale of 1 to 5.
C - Tear Resistance
Based on the amount of force required to tear the sample. The protection factor is then expressed on a scale of 1 to 4.
D - Puncture Resistance
Based on the amount of force required to pierce a sample with a standard sized tip. The protection factor is then expressed on a scale of 1 to 4.
NOTE: A result marked with an X indicates that the glove was not tested for the hazard; it was not tested; a result marked with an O indicates that the glove failed the test.
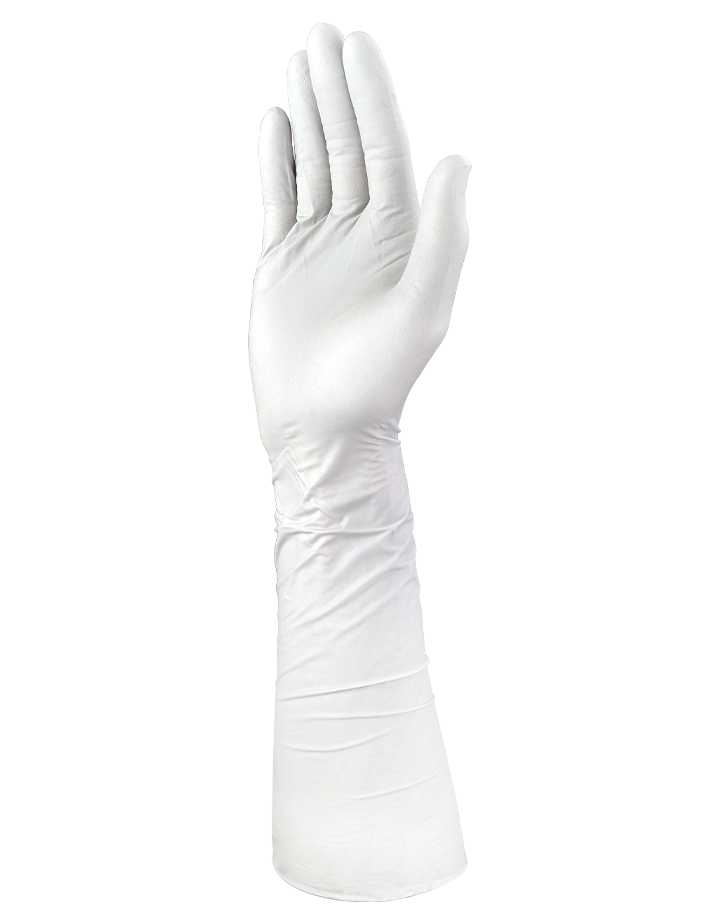
EN ISO 21420: 2020:Protective gloves - General requirements and test methods
The EN ISO 21420: 2020 standard aims to ensure that the glove itself does not cause harm to the wearer, is comfortable to wear, and does not interfere with the protective performance of the user.
Tests and requirements include chemical harmlessness of glove materials (including pH, hexavalent chromium, azo dyes, polycyclic aromatic hydrocarbons nickel release and DMFa, etc.), and optional requirements for water vapor transmission and absorption of materials, as well as wearing and new considerations for taking off layered glove. Also included is a procedure to examine glove size and its effect on finger dexterity.
The EN ISO 21420:2020 standard also outlines general requirements for the information to be provided and marked on gloves.
EN ISO 21420 test item requirements:
1. Glove Design and Construction
Clause 4.1 outlines requirements and guidelines for glove design and construction, this guideline describes that protective gloves must not interfere with the performance of the activity while providing adequate risk protection.
A new consideration under EN ISO 21420 is the donning and doffing of protective gloves. During these operations, reusable multi-layer gloves must not separate, and gloves must be designed to minimize the time required for donning and doffing.
2. Harmless
Chemical harmlessness is considered to ensure that protective gloves do not adversely affect the health or hygiene of the wearer. Under normal foreseeable conditions of use, materials in gloves shall not release substances that are generally known to be toxic, reproductively toxic, carcinogenic, mutagenic, allergenic, corrosive, sensitizing or irritating. This is outlined in clause 4.2 of the standard.
Requirements include:
1. Hexavalent chromium - applicable to all leathers; less than 3mg/kg
2. Nickel release - for metal parts in prolonged contact with the skin; less than 0.5µg/cm 2 /week
3. pH value - applicable to all materials; requirements: pH value greater than 3.5 and less than 9.5. Each material must be tested individually
4. Azo colorants - suitable for all dyed leather and textiles;
5. Requirements: Each carcinogenic aromatic amine listed in the analytical method dimethylformamide (DMFa) is less than 30mg/kg - applicable to all materials containing polyurethane (PU); less than 1,000 mg/kg (1 % w/w)
6. Polycyclic Aromatic Hydrocarbons (PAHs) – For rubber and plastics that come into direct skin contact; each of the eight restricted PAHs is less than 1mg/kg.
3. Comfort and efficiency
Clause 5 of EN ISO 21420 outlines the requirements for glove size and dexterity. Dexterity is defined as "the ability to manipulate the hands to perform tasks."
Sizing is defined by the size of the palm that the glove will fit. Sizes listed under this standard cover the range from 4 to 13. Evaluation criteria for size compliance include hand circumference and hand length (distance from wrist to tip of middle finger).
A minimum glove length can be defined and measured if required for a specific application (eg welder's gloves or firefighter's gloves). However, this is not specified in the general requirements for gloves. Beyond that, different dimensioning systems may be used if explained in the terms of EN ISO 21420:2020. This information needs to be listed on the user information sheet provided with the protective glove.
The dexterity of a glove depends on a variety of factors, including the thickness and elasticity of the glove material. In evaluating the dexterity of the gloves, four gloves were tested. Dexterity is graded based on the diameter of the smallest steel needle that can be picked up from a flat surface 3 times within 30 seconds. If the needle cannot be picked up, the level reached is zero. Finger dexterity can be assessed for specific uses if desired.
Changes from EN 420:2003+A1:2009:
Notified bodies should take into account changes or additions to EN 420:2003+A1:2009 when assessing applications for certification in order to update the technical file for gloves that have been type-approved using EN 420:2003+A1:2009:
1. Reusable multi-layer gloves must be removed without layering as described in Section 4.1
2. No longer includes the waterproof performance level of the glove material. Depending on the intended use of the glove, this test is optional in EN 420
3. Gloves intended to be worn in areas where there may be a risk of flammability or explosion require electrostatic performance testing according to EN 16350. Previously (in EN 420), the referenced test method was EN 1149 Part 1, 2 or 3, electrostatic pictograms could not be used
4. It is important to note that a list of known allergens present in protective gloves will be provided if required, a list of such substances can be found in EN ISO 21420 Annex G.
There have also been some changes to the chemically innocuous requirements for gloves. First, determining the presence of extractable proteins in natural rubber latex gloves is no longer listed as a mandatory assessment. However, for gloves containing any natural rubber, a warning must be included ("Gloves contain natural rubber which may cause an allergic reaction"). Additionally, there are new requirements to test for the presence of nickel release, azo colorants, DMFa and PAH.
Due to the growing number of sustainable development initiatives, other environmental aspects (outlined in Annex F) also need to be considered. EN ISO 21420 also references REACH and the Classification, Labeling and Packaging (CLP) regulations for hazardous substances to ensure that chemical harmlessness assessments are kept up to date with the latest chemical restrictions.
Tests and requirements include chemical harmlessness of glove materials (including pH, hexavalent chromium, azo dyes, polycyclic aromatic hydrocarbons nickel release and DMFa, etc.), and optional requirements for water vapor transmission and absorption of materials, as well as wearing and new considerations for taking off layered glove. Also included is a procedure to examine glove size and its effect on finger dexterity.
The EN ISO 21420:2020 standard also outlines general requirements for the information to be provided and marked on gloves.
EN ISO 21420 test item requirements:
1. Glove Design and Construction
Clause 4.1 outlines requirements and guidelines for glove design and construction, this guideline describes that protective gloves must not interfere with the performance of the activity while providing adequate risk protection.
A new consideration under EN ISO 21420 is the donning and doffing of protective gloves. During these operations, reusable multi-layer gloves must not separate, and gloves must be designed to minimize the time required for donning and doffing.
2. Harmless
Chemical harmlessness is considered to ensure that protective gloves do not adversely affect the health or hygiene of the wearer. Under normal foreseeable conditions of use, materials in gloves shall not release substances that are generally known to be toxic, reproductively toxic, carcinogenic, mutagenic, allergenic, corrosive, sensitizing or irritating. This is outlined in clause 4.2 of the standard.
Requirements include:
1. Hexavalent chromium - applicable to all leathers; less than 3mg/kg
2. Nickel release - for metal parts in prolonged contact with the skin; less than 0.5µg/cm 2 /week
3. pH value - applicable to all materials; requirements: pH value greater than 3.5 and less than 9.5. Each material must be tested individually
4. Azo colorants - suitable for all dyed leather and textiles;
5. Requirements: Each carcinogenic aromatic amine listed in the analytical method dimethylformamide (DMFa) is less than 30mg/kg - applicable to all materials containing polyurethane (PU); less than 1,000 mg/kg (1 % w/w)
6. Polycyclic Aromatic Hydrocarbons (PAHs) – For rubber and plastics that come into direct skin contact; each of the eight restricted PAHs is less than 1mg/kg.
3. Comfort and efficiency
Clause 5 of EN ISO 21420 outlines the requirements for glove size and dexterity. Dexterity is defined as "the ability to manipulate the hands to perform tasks."
Sizing is defined by the size of the palm that the glove will fit. Sizes listed under this standard cover the range from 4 to 13. Evaluation criteria for size compliance include hand circumference and hand length (distance from wrist to tip of middle finger).
A minimum glove length can be defined and measured if required for a specific application (eg welder's gloves or firefighter's gloves). However, this is not specified in the general requirements for gloves. Beyond that, different dimensioning systems may be used if explained in the terms of EN ISO 21420:2020. This information needs to be listed on the user information sheet provided with the protective glove.
The dexterity of a glove depends on a variety of factors, including the thickness and elasticity of the glove material. In evaluating the dexterity of the gloves, four gloves were tested. Dexterity is graded based on the diameter of the smallest steel needle that can be picked up from a flat surface 3 times within 30 seconds. If the needle cannot be picked up, the level reached is zero. Finger dexterity can be assessed for specific uses if desired.
Changes from EN 420:2003+A1:2009:
Notified bodies should take into account changes or additions to EN 420:2003+A1:2009 when assessing applications for certification in order to update the technical file for gloves that have been type-approved using EN 420:2003+A1:2009:
1. Reusable multi-layer gloves must be removed without layering as described in Section 4.1
2. No longer includes the waterproof performance level of the glove material. Depending on the intended use of the glove, this test is optional in EN 420
3. Gloves intended to be worn in areas where there may be a risk of flammability or explosion require electrostatic performance testing according to EN 16350. Previously (in EN 420), the referenced test method was EN 1149 Part 1, 2 or 3, electrostatic pictograms could not be used
4. It is important to note that a list of known allergens present in protective gloves will be provided if required, a list of such substances can be found in EN ISO 21420 Annex G.
There have also been some changes to the chemically innocuous requirements for gloves. First, determining the presence of extractable proteins in natural rubber latex gloves is no longer listed as a mandatory assessment. However, for gloves containing any natural rubber, a warning must be included ("Gloves contain natural rubber which may cause an allergic reaction"). Additionally, there are new requirements to test for the presence of nickel release, azo colorants, DMFa and PAH.
Due to the growing number of sustainable development initiatives, other environmental aspects (outlined in Annex F) also need to be considered. EN ISO 21420 also references REACH and the Classification, Labeling and Packaging (CLP) regulations for hazardous substances to ensure that chemical harmlessness assessments are kept up to date with the latest chemical restrictions.
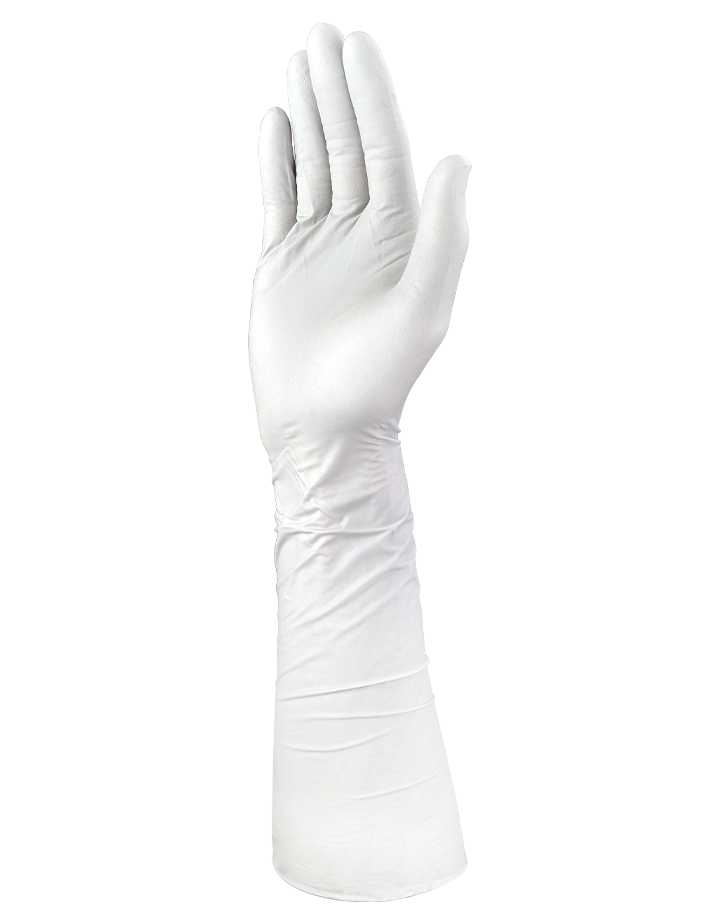